Circularity plans for textile products
Circularity plans for textile products
In a world that increasingly demands environmental responsibility, textile recycling has become an essential step towards a sustainable future.
At INTERZERO we accompany you in the design and execution of textile recycling projects that not only contribute to the circular economy, but also rigorously comply with all current regulations.
Our experience in waste management and extended producer responsibility (EPR) allows us to offer comprehensive solutions tailored to your company's needs. We take care of the entire process: from project planning, collection and sorting of materials, to recovery or proper disposal of textiles. In addition, we ensure that all activities are carried out in accordance with local, national and international laws governing textile waste management.
With our services, your company will not only reduce its environmental impact, but also strengthen its corporate image, demonstrating a real commitment to sustainability. We manage regulatory compliance from start to finish: we help you obtain the necessary licences, register your products in accordance with current legislation and submit the mandatory reports to the relevant authorities.
From reusing fibres in new products to creating innovative sustainable fashion lines, our projects give you a competitive edge in a market that increasingly values social and environmental responsibility.
At INTERZERO, we believe in a waste-free future. We invite you to be part of the change, driving textile recycling projects that make a difference. Our team of experts is ready to advise you at every stage, ensuring that your initiative is not only successful, but also fully compliant.
Become a protagonist of sustainable transformation.
Contact us and start your compliant textile recycling project today.
Talking about the future of Accenture
What we need is: courage, curiosity and data.
How can we lighten the burden on the planet? The best way is to do it together. Britta von Selchow of Interzero and renowned sustainability expert Sabine Braun of Accenture discuss why companies should move to a circular economy now.
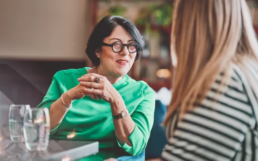
Britta von Selchow: Ms Braun, you have been advising companies on sustainability issues for 30 years, and the topic is still far from reality. Where are we today, especially when it comes to the circular economy?
Sabine BraunSustainability has long been more than just a hygiene factor for companies. Transparency alone is no longer enough. Many are aware that this is now a real transformation, that they need new raw material perspectives and that they must change their business models. However, there is some hesitation, which is a pity. The circular economy can make an important contribution to climate protection. But it is still a sleeping giant, with enormous untapped potential.
Britta von Selchow: What do companies need to act now to realise their potential?
Sabine Braun: The Green Deal and EU legislation are paving the way. But it is not only grand visions, such as climate neutrality by 2050, that are important. To achieve them, companies need concrete strategies, as well as courage, curiosity and perseverance. When, if not now, should companies invest? In any case, the circular revolution is coming, and who wants to be among the losers?
Britta von Selchow: Keeping raw materials in circulation and being able to reuse them for our own production: in our experience, this is increasingly important for manufacturers for three reasons. To meet regulatory requirements, to increase our resilience to supply chain fluctuations in a country like Germany, which is poor in raw materials, and, last but not least, to gain cost advantages by reusing components. Successful cycles are created through the cooperation of the participants in the value chain. Openness and the ability to cooperate are important core competencies of our future.
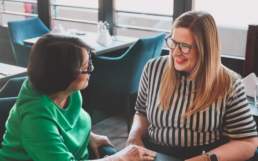
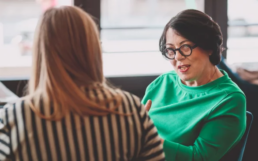
Sabine Braun: In any case, the ability to think in terms of economic ecosystems is a key factor for success. Creating closer networks, harnessing the innovative capacity of start-ups and developing multi-company industrial solutions: of course, none of this works at scale without digitalisation and artificial intelligence.
Britta von Selchow: We are also firmly convinced of this and have therefore developed a digital twin of the recycling process chain: Materialkonto Interzero. This means that companies can now map the entire raw material cycle. In this way, production waste and products and their packaging are effectively returned to their own cycle at the end of their useful life.
Sabine Braun: I am certain that digital solutions, such as those promoted by Interzero, are key to the progress of the circular economy and sustainable transformation as a whole. This applies not only to the upcoming reporting obligations - keyword CSRD. Sustainability data is becoming increasingly important as a control element for companies. In the future, no one will be able to avoid it.
Britta von Selchow: How do you motivate companies to actively shape the future, and perhaps get out of their comfort zone?
Sabine Braun: In the case of the "call to action", just look at the facts. If you want your children and grandchildren to continue to have a liveable planet, you need to act now. To do this, we need a positive narrative about the future. We have incredible knowledge and experience, a great medium-sized company. Germany is a country of ideas that must finally get out on the streets.
Britta von Selchow: The good news is that no one has to save the world alone. Closing cycles is a team sport that brings fun and enthusiasm. I experience this positive spirit in our company and also among our customers. With the right partners, courage, curiosity and data, sustainable value creation can be achieved. Intelligent, digitally optimised recycling creates new perspectives on the raw materials we all urgently seek.
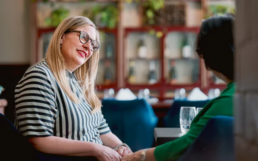
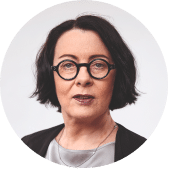
"The circular economy is a sleeping giant with huge untapped potential".
Sabine Braun
Accenture Sustainability Strategy and Consulting
Contact
Knowledge library
Knowledge library
Welcome to our sustainability news and media centre. Here you will find a source of information to help you stay up to date and explore the most important issues about a sustainable future.
About us
Let's build a waste-free future together.Zero Waste Solution
Contact
PET recycling partnership
Partnership for greater PET recycling
In collaboration with the non-profit organisation COREPLA, Interzero has launched a pilot project in Italy to return PET bottle deposits. With remarkable success.
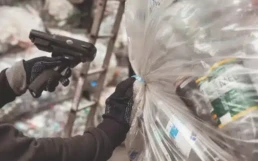
Beverage container deposit systems have been in place in Germany for a long time. The single deposit for PET bottles, for example, actively contributes to the avoidance of plastic waste and the recovery of raw materials for high-quality bottle-to-bottle recycling. The introduction of bottle return systems has also gained momentum in other European countries. Ultimately, it is important to reach the ambitious EU collection targets and to prepare for a possible Europe-wide deposit obligation from 2028. The countries that currently lack a legally established packaging return system are Poland and Italy. In both countries, Interzero supports its partners to close the loop, through advice, exchange of experience and specific projects.
PET collection project in Italy: Together with COREPLA, the leading national consortium for the collection and recycling of plastic packaging, Interzero launched an ambitious nationwide pilot project in Italy in 2022. The collaborating partners aimed to ensure comprehensive collection, traceability of PET streams and scalability of the solution. In the first phase, more than 100 returnable vending machines were installed in the outlets of major retailers. To motivate consumers to return empty PET bottles, Interzero also developed an app through which users can collect bonus points and redeem them for shopping vouchers.
The project was an immediate success: by the end of 2023 Italy reached an impressive collection rate of 78% of PET bottles on the market, already exceeding the EU requirement of 77% by 2025. COREPLA has received EU funding to expand existing capacity; an additional 1,000 recyclers will be installed in retail outlets within three years. Interzero Italy also benefits: "We have created a win-win partnership that reinforces our strategic positioning and demonstrates our proven expertise in innovative business solutions," says Sergio Patacchini, project manager at COREPLA. - says Sergio Patacchini, project manager at Interzero Circular Solutions Italy. The experience gained is a good basis for the further successful implementation of the project, and perhaps to support the implementation of the bail system on a national scale.
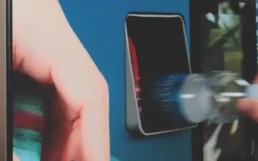
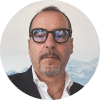
"We have created a win-win partnership that strengthens our strategic position and demonstrates our proven expertise in innovative business solutions.
Sergio Patacchini
Contact
Chemical recycling
Chemical recycling: The best for the rest
The ideal complement to mechanical recycling: our sorting plant in Walldürn will enable large-scale chemical recycling of plastics. The raw materials are protected from burning and processed into high-quality products.
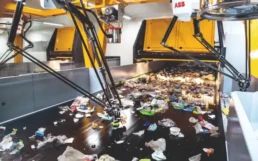
At present, the only option for mixed plastic waste that cannot be mechanically recycled is often incineration. To keep these raw materials in circulation, recycling companies, the petrochemical industry and plastics manufacturers are working together to expand chemical recycling. This has potential: "Chemical recycling can handle material streams that cannot be recycled mechanically and thus save resources and avoid incineration," says Dr. Markus Hiebel, Head of Sustainability and Participation at the Fraunhofer Institute for Environment, Safety and Energy Technology UMSICHT.
Mixed plastics in the spotlight
Every year, Interzero processes more than 800,000 tonnes of light packaging in yellow bags and yellow containers. Approximately half of this is recycled mechanically and used, for example, to produce regranulates for the plastics industry. A quarter consists of sorting waste, including "unsuitable waste", which should not go into the yellow bin. The remaining 25% is made up of mixed plastics that cannot be clearly attributed to the sorting fraction and which previously went for thermal recycling. Interzero has developed a new sorting process just for this mix of materials. "Whereas our previous sorting systems focused on mono-materials such as PE and PP, we are using the new technology to generate plastic streams precisely tailored to our partners' chemical recycling processes," explains Dr. Richard von Goetze, CEO of Interzero. - explains Dr. Richard von Goetze, Interzero's chemical recycling manager.
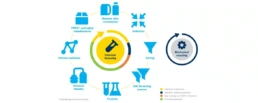
Production in Walldürn is scheduled to start in 2026.
In November 2023, construction work will begin in Walldürn (Baden-Württemberg) on Europe's largest sorting plant for the production of raw materials for chemical recycling, a joint venture of Interzero and OMV. With this project, the partners are creating around 120 new jobs and new prospects for a circular economy. Once production starts in 2026, the plant will process up to 260,000 tonnes of mixed used plastics per year. "We assume that we will be able to recover such large volumes for chemical recycling" - says Dr. Richard von Goetze - "This will enable our partner companies to produce new food-grade plastics".
New plastics from non-recyclable waste plastics
OMV, for example: The company will process mixed plastics from a common Walldürn sorting plant in its ReOil® plant, where these mixed plastics are broken down again into their basic components by pyrolysis. The pilot plant can transform 100 kilograms of used plastics into 100 litres of pyrolysis oil per hour. Another plant with a capacity of 16,000 tonnes per year is currently under construction at the OMV plant in Schwechat (Lower Austria). The next step is the development of an industrial-scale ReOil® plant with a planned capacity of up to 200,000 tonnes per year. The recovered raw materials will be used to produce plastics for a wide range of applications. The plastics will be ISCC PLUS certified (International Sustainability & Carbon Certification), which provides traceability throughout the supply chain and ensures that the value chain meets all environmental and social standards.
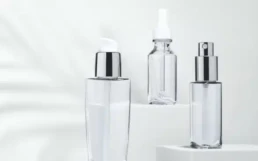
Sustainable partnership with Eastman
Different process, same goal: together with the US company Eastman, Interzero is opening up a new way of recycling difficult-to-recycle PET containers. The company's future molecular recycling plant in France should be able to process more than 200,000 tonnes of PET waste per year. "Interzero and Eastman are committed to reducing plastic waste and building a closed loop," says Reinier de Graaf, director of raw materials strategy at Eastman. "We are pleased to work closely with Interzero to source some of the raw materials needed for our plant. Eastman's polyester processing technology allows mixed PET waste to be broken down into monomers and then recombined into a high-quality material.
Thanks to the efficiency of the integrated plant and the renewable energy sources available in France, the plant is expected to operate with significantly lower greenhouse gas emissions than conventional oil-based processes. The concept is also well received by brand manufacturers - Eastman already produces on a large scale in the US and sells its recycled materials worldwide: Eastman's recycled plastics are transformed into reusable bottles, household appliances, consumer electronics and cosmetics packaging, among others. The French project is also receiving strong support from global brands, including LVMH Beauty, The Estée Lauder Companies, Clarins, Procter & Gamble, L'Oreal and Danone, which have signed letters of intent for multi-year supply agreements.
Next steps
Working together to close the loop and secure valuable raw materials: The industry offers new technologies and opportunities, but the expansion of chemical recycling will also depend on the political framework conditions, e.g. recognition in the Packaging Act. Dr. Axel Schweitzer, CEO and shareholder of Interzero, said at the groundbreaking ceremony for the new plant in Walldürn: "I am convinced that, with chemical recycling, the recycling rate in Germany can and will increase significantly in the future. This will bring us a big step closer to our vision of a waste-free world."
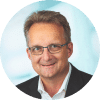
"In Interzero we see a promising cooperation partner with many years of experience, with whom we would like to invest together in an innovative future that enables a more complete closed-loop economy for plastic waste."
Maximilian Grasserbauer
Contact
PET recycling in Liebenau
PET recycling - things are going well in Liebenau
In Interzero's new PET recycling plant, shredded returnable bottles are converted into food-grade granules for the beverage industry.
Swapping the old for the new: when it comes to recycling PET beverage bottles from the deposit system, this can be taken literally. A look at Interzero's new plant in Liebenau, Lower Saxony, shows what is possible today with state-of-the-art processes. What you don't see here, however, are empty bottles. The material had already gone through several processing steps when it was delivered here. The collected PET bottles have been previously shredded, sorted by material and colour and then cleaned by scalding.
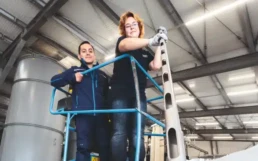
1. Delivery and quality control
The so-called PET flakes arrive at the recycling plant in 1,000 kg big bags. The Interzero team takes a sample from every second bag, examines the material for contaminants and analyses the chemical residues, moisture content and viscosity. The actual processing only begins when quality control gives the green light.
2. Homogenisation
The flakes are first homogenised in mixing silos to absorb fluctuations in the material composition and thus stabilise the downstream processes. The screw conveyor then moves on to a further, even more precise sorting stage. Interzero uses near infrared (NIR) technology for this purpose.
3. near infrared separator
The NIR separator is fully automated and separates impurities and unwanted colours such as green, yellow or dark blue. Only light blue flakes are allowed to remain in the process, as they positively affect the light colour shades required for competitive production grade plastics.
4. Extrusion
Now the actual extrusion phase begins, which converts the pre-treated PET flakes into high-quality granulate for production. For this purpose, the plastic is melted at about 290 °C and fed into another screw conveyor. This viscous mass passes through several filters before finally passing through a perforated panel to be shredded by a granulator. In order to make the granulate suitable for use as a food contact material, a final processing step is necessary, which takes place in a solid state polycondensation (SSP) reactor. The material remains in the reactor for about 10 hours at a temperature of about 180°C in a vacuum/nitrogen atmosphere, which allows the oxygen molecules to escape and prevents undesirable reactions with the material.
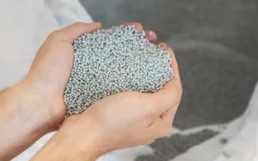
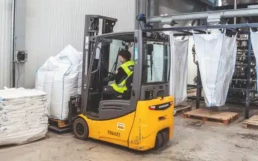
5. Return to traffic
The finished granules are put back into big bags and sent for further processing. Interzero customers use food-grade rPET to produce so-called "preforms". These "raw bottles" are produced by injection moulding and look a bit like test tubes: they can be blown into full-size bottles and, once filled, end up back on shop shelves, completing the bottle-to-bottle cycle. The cycle starts again when consumers return their bottles to collect the deposit.
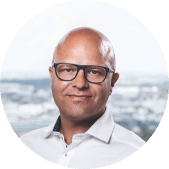
"This plant gives us the opportunity to sell recycled PET pellets for food contact, which we produce in-house. This 'closes the loop' here in Germany, a real sustainability benefit for our customers."
Romed Aspmair
Managing Director, RDB plastics GmbH
Facts and figures
Compact bottle-to-bottle recycling: the plant can recycle a total of 12,000 tonnes per year.
Recycling is carried out under vacuum and part of the process uses a nitrogen atmosphere. This process step ensures that the material stream is free of moisture and undesirable substances that off-gas when the plastic is heated.
A key advantage for beverage customers: the plant is accredited by the European Food Safety Authority (EFSA).